Oven Temperature Data Logger Logs in Extreme Heat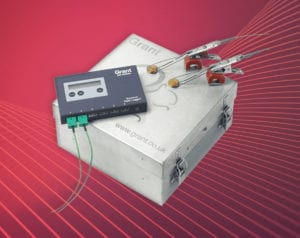
CAS DataLoggers provided the oven temperature data logging solution for a supplier of raw materials used in the plastics rotary molding industry. This company offers a comprehensive technical support service to their customer base, and part of this service includes technical advice and assistance for maximizing the rotational molding process to increase customer production efficiency.
Previously, the company had relied on a simple, single-channel data logger, but this unit was adversely affected by the high operating temperatures since it was enclosed in a low-quality thermal barrier. Their logger simply could not offer the robustness or longevity required by the customer, nor could it effectively log the temperature profile of the mold tool using just a single channel. Therefore the supplier required a multi-channel solution with adequate protection for years of operation.
Installation
CAS DataLoggers provided the customer with a Grant OMK610 Oven Temperature Profile Data Logger along with a custom enhanced thermal barrier for effective heat absorption. Users connected four Type K thermocouples to the data logger to monitor the internal temperature of the molding tool when inside the curing oven. The thermocouples were wired to the inside of the mold tool to monitor the air temperature and crystallization point of the polymer material which is 180oC (356oF). This process monitoring aids their customer’s QA processes and assists them in minimizing the curing time while ensuring that the product is not over-cured, preventing a significantly detrimental effect on product appearance and quality.
Usage
Designed for temperature and rotational molding process monitoring, the logger’s six thermocouple inputs accommodated both Type T and Type K thermocouple probes and supported high sample rates up to eight samples a second, supporting fast process times. During production runs, the barrier’s all-stainless steel construction formed a robust barrier for the data logger. For extended logging, the thermal barrier could be used to up to 250oC (482oF) for up to 20 minutes depending upon the size and volume of the oven cavity.
With each reading, the Grant data logger reported and stored the time and date onto non-volatile memory holding up to 260,000 readings of secure data. Being battery-operated and portable, the oven logger operated in stand-alone fashion. Users navigated the menus through the intuitive 3-button design via the integrated display, and these were also navigable via PC. The logger was able to be configured to start and stop recording automatically at user-set times and temperature levels to present the most accurate process overview.
Passing through the process along with the products, the logger created a temperature profile which gave users a detailed view of their heat curing process. For example, percentage cure results were shown on screen at the end of every run and were available for storage and later analysis.
Benefits
The customer can now optimize their process by reducing production cycle times while maintaining their high quality of production. This increase in yield reduces their manufacturing costs. In addition, using the included software, they are now able to document batch-to-batch thermal processing and print reports to validate that the product has been produced in accordance with their QA and product procedures. The kit was also cost-effective for this application, including the thermal barrier at a price less than competing models.
For more information on the Grant OMK610 Oven Temperature Profile Data Logger, the rotational molding process or to find the ideal solution for your performance monitoring needs, contact a CAS Data Logger Applications Specialist at (800) 956-4437 or request more information.